Ensuring Safety: The Importance of Test and Tagging Compliance Check
Introduction
Understanding Test and Tagging
Test and Tagging is a crucial process in ensuring the safety of electrical equipment in workplaces. It involves inspecting, testing, and tagging electrical appliances to ensure they are safe for use. This process is especially important in environments where electrical equipment is regularly used, such as offices, construction sites, factories, and schools. Test and Tagging: Compliance Check
The Importance of Compliance Check
Legal Requirements
Ensuring compliance with test and tagging regulations is not just a matter of best practice; it is often a legal requirement. Occupational Health and Safety (OHS) regulations in many jurisdictions mandate regular testing and tagging of electrical appliances to prevent accidents and ensure workplace safety. Failure to comply with these regulations can result in fines, legal liability, and even the closure of businesses.
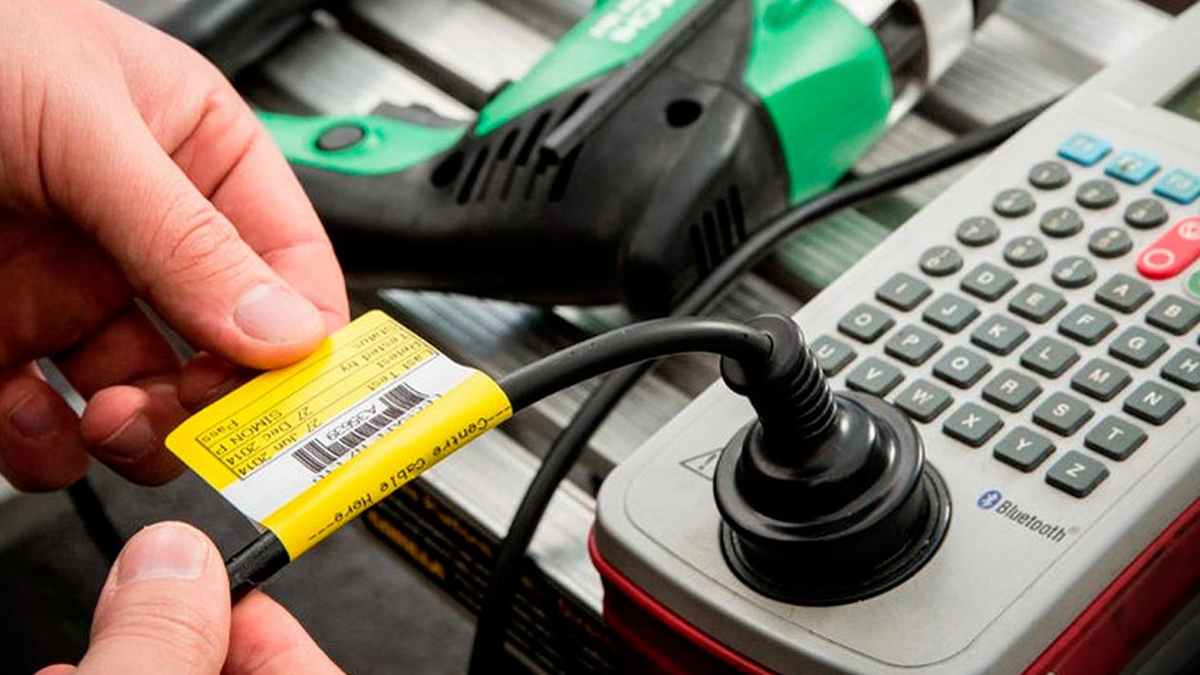
Risk Mitigation
Regular compliance checks through test and tagging help mitigate the risk of electrical accidents. Faulty electrical appliances can pose serious hazards, including electric shocks, fires, and even fatalities. By identifying and rectifying faults through testing and tagging, businesses can significantly reduce the likelihood of such incidents occurring, thereby safeguarding the well-being of employees and visitors.
Insurance Requirements
Insurance providers often require businesses to comply with test and tagging regulations as part of their risk management protocols. Failure to meet these requirements can lead to insurance claims being denied in the event of an electrical accident. By conducting regular compliance checks, businesses not only ensure the safety of their premises but also maintain eligibility for insurance coverage.
The Test and Tagging Process
Inspection
The test and tagging process begins with a visual inspection of electrical appliances. This involves checking for any visible signs of damage, wear, or defects. Common issues to look out for include frayed wires, cracked casings, loose connections, and missing insulation. Any appliances found to have visible faults should be immediately removed from service and repaired or replaced.
Testing
Following the visual inspection, electrical appliances undergo electrical testing using specialized equipment. This testing assesses various electrical parameters, including insulation resistance, earth continuity, and polarity. The results of these tests determine whether the appliance is safe for use or requires further attention. Testing should be conducted by trained professionals using calibrated testing equipment to ensure accuracy and reliability.
Tagging
Once an electrical appliance has been inspected and tested, it is tagged with a label indicating its compliance status. These tags typically include information such as the date of testing, the name of the tester, and the next scheduled test date. Green tags are used to signify that the appliance has passed the test and is safe for use, while red tags indicate that the appliance has failed and must be repaired or replaced.
Compliance Best Practices
Regular Testing Schedule
Establishing a regular testing schedule is essential for maintaining compliance with test and tagging regulations. The frequency of testing depends on various factors, including the type of appliance, its environment, and its usage patterns. Generally, high-risk appliances should be tested more frequently than low-risk ones. Businesses should create a testing schedule based on these factors and adhere to it rigorously.
Documentation
Accurate record-keeping is crucial for demonstrating compliance with test and tagging regulations. Businesses should maintain detailed records of all inspections, tests, and repairs conducted on electrical appliances. This documentation should include information such as the appliance’s serial number, make and model, testing results, and any remedial actions taken. Keeping comprehensive records not only helps ensure compliance but also facilitates traceability and accountability.
Training and Certification
Ensuring that personnel responsible for conducting test and tagging are adequately trained and certified is essential for maintaining compliance. Training programs should cover topics such as electrical safety principles, testing procedures, and regulatory requirements. Certification programs provide validation of competence and proficiency in conducting test and tagging activities. By investing in training and certification for staff, businesses can enhance the effectiveness and reliability of their compliance efforts.
Conclusion
Prioritizing Safety through Compliance
Test and tagging compliance checks are indispensable for safeguarding against electrical hazards in the workplace. By adhering to regulatory requirements, implementing best practices, and prioritizing safety, businesses can create safer work environments, protect against legal liabilities, and mitigate the risk of accidents. Investing in test and tagging compliance is not just a legal obligation but a fundamental commitment to the well-being of employees and the sustainability of businesses.